2016 augusztusának elején az amerikai haditengerészet sikeresen tesztelte az Osprey MV-22 rotor-t. Ez a repülőgép önmagában nem szokatlan. Az ikerrotoros jármű már régóta szolgálatban áll az amerikai haditengerészetnél (az 1980-as évek második felében helyezték üzembe), de a történelem során először a kritikus alkatrészeket egy tiltrotorra szerelték fel (repülésbiztonság közvetlenül tőlük függ), amelyek 3D nyomtatott nyomtatók voltak.
A teszteléshez az amerikai hadsereg egy konzolt nyomtatott a motornak a rotátor szárnyához való rögzítéséhez titánból közvetlen rétegréteg lézeres szinterezéssel. Ezzel egyidejűleg magára a konzolra egy feszültségmérőt szereltek, amelynek célja az alkatrész esetleges deformációjának regisztrálása. Az Osprey MV-22 rotor két motorja mindegyike négy ilyen konzol segítségével van a szárnyhoz rögzítve. Ugyanakkor a tiltrotor első próbarepülése idején, amely 2016. augusztus 1 -én történt, csak egy, 3D nyomtatón nyomtatott konzol volt felszerelve rá. Korábban arról számoltak be, hogy a háromdimenziós nyomtatás módszerével kinyomtatott szemcseszerelvényeket is a tiltrotorra szerelték fel.
A tiltrotorhoz nyomtatott alkatrészek fejlesztését az amerikai haditengerészet légiközlekedési harci műveleti központja végezte, amely a New Jersey állambeli McGuire-Dix-Lakehurst közös bázison található. Az Osprey MV-22 nyomtatott alkatrésszel végzett repülési tesztjeit az amerikai haditengerészet Patxent River bázisán végezték, a teszteket a hadsereg teljesen sikeresnek ismerte el. Az amerikai hadsereg úgy véli, hogy a háromdimenziós nyomtatás széles körű bevezetésének köszönhetően a jövőben a technológia képes lesz gyorsan és viszonylag olcsón előállítani az átalakítók alkatrészeit. Ebben az esetben a szükséges részletek közvetlenül a hajókra nyomtathatók. Ezenkívül a nyomtatott részek módosíthatók a fedélzeti szerelvények és rendszerek teljesítményének javítása érdekében.
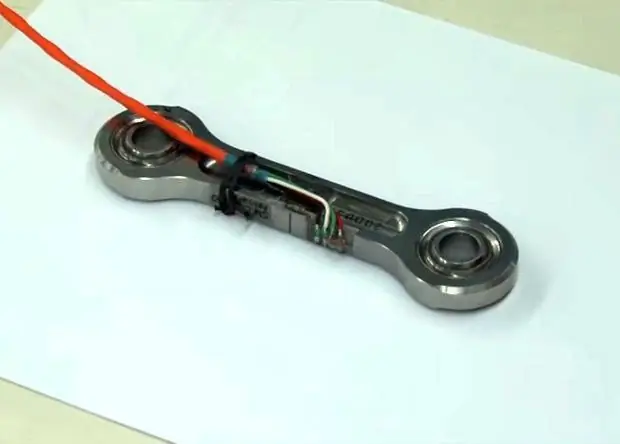
Titán nyomtatott motorra szerelhető konzol
Az amerikai hadsereget néhány évvel ezelőtt érdekelték a 3D nyomtatási technológiák, de a közelmúltig a 3D nyomtatók funkcionalitása nem volt elég széles ahhoz, hogy rutinszerűen használhassák meglehetősen összetett alkatrészek gyártásához. A tiltrotor alkatrészeit egy additív 3D nyomtató segítségével hozták létre. Az alkatrész fokozatosan rétegekben készül. A titánpor három rétegét lézerrel kötik össze, ezt az eljárást addig ismételjük, ameddig szükséges a kívánt forma eléréséhez. A befejezés után a felesleget levágják az alkatrészről; a kapott elem teljesen használatra kész. Mivel a teszteket sikeresen befejezték, az amerikai hadsereg nem áll meg itt, hanem a tiltrotor 6 fontosabb szerkezeti elemét fogják megépíteni, amelyek fele szintén titán, a másik pedig acél lesz.
3D nyomtatás Oroszországban és világszerte
Annak ellenére, hogy a nyomtató típusú gyártást néhány évvel ezelőtt sikeresen végrehajtották az USA -ban és Oroszországban, a katonai felszerelésekhez szükséges elemek létrehozása folyamatban van. Először is ennek köszönhető az összes katonai termékre vonatkozó nagyon magas követelmények, elsősorban a megbízhatóság és a tartósság tekintetében. Az amerikaiak azonban nincsenek egyedül ezen a területen. Az orosz tervezők immár második éve gyártanak alkatrészeket a kifejlesztett rohampuskákhoz és pisztolyokhoz 3D nyomtatási technológia segítségével. Az új technológiák értékes rajzolási időt takarítanak meg. Az ilyen alkatrészek sugárzása pedig gyors cserét biztosíthat a terepen, a javító zászlóaljakban, mivel nem kell várni a gyárból származó alkatrészekre ugyanazokhoz a tankokhoz vagy pilóta nélküli légi járművekhez.
A tengeralattjárók számára a katonai 3D nyomtatók egyszerűen aranyat érnek majd, mivel autonóm távolsági navigáció esetén az alkatrészek cseréje magukra a tengeralattjárókra szinte kimeríthetetlen erőforrást biztosít a tengeralattjárónak. Hasonló helyzet figyelhető meg a hosszú utakat végző hajók és a jégtörők esetében. A legtöbb ilyen hajó drónokat kap a közeljövőben, amelyek végül javítást vagy teljes cserét igényelnek. Ha a hajón megjelenik egy 3D nyomtató, amely lehetővé teszi a pótalkatrészek gyors nyomtatását, akkor néhány óra múlva a berendezés újra használható. A műveletek mulandóságának és a katonai műveletek színházának nagy mobilitásának körülményei között bizonyos alkatrészek, szerelvények és mechanizmusok helyszíni összeszerelése lehetővé teszi a támogató egységek magas szintű hatékonyságának fenntartását.
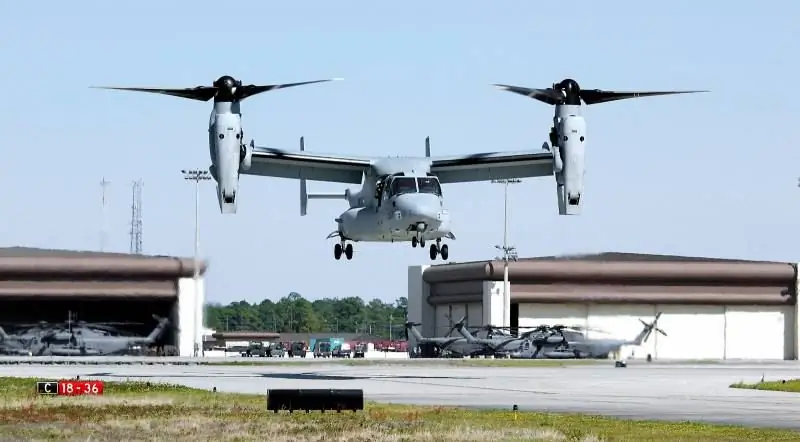
Osprey MV-22
Miközben az amerikai hadsereg elindítja kabriógépeit, az Armata tank orosz gyártói már második éve használnak ipari nyomtatót Uralvagonzavodban. Segítségével páncélozott járművek alkatrészeit, valamint polgári termékeket állítanak elő. De eddig az ilyen alkatrészeket csak prototípusokhoz használják, például az Armata tank létrehozásában és tesztjeiben. A Kalasnyikov Konszernen, valamint a TsNIITOCHMASH -on az orosz hadsereg megrendelésére a tervezők 3D -s nyomtatók segítségével fém- és polimerforgácsokból készítenek kézifegyverek különböző részeit. Nem marad el tőlük a Shipunovról elnevezett Tula Instrument Design Bureau, a híres CPB, amely a gyártott fegyverek gazdag választékáról ismert: a pisztolyoktól a nagy pontosságú rakétákig. Például egy ígéretes pisztolyt és egy ADS rohamfegyvert, amely az AK74M és az APS különleges erők helyettesítésére szolgál, nagy szilárdságú műanyag alkatrészekből állítják össze, amelyeket nyomtatóra nyomtatnak. Néhány katonai termék esetében a CPB már képes volt formákat készíteni; jelenleg a termékek sorozatos összeszerelése folyik.
Olyan körülmények között, amikor új fegyverkezési versenyt figyelnek meg a világban, az új típusú fegyverek megjelenésének időzítése válik fontossá. Például páncélozott járművekben általában csak egy modell létrehozása és a rajzokból prototípusba történő átvitele folyik általában egy -két évig. Tengeralattjárók fejlesztésekor ez az időszak már kétszer hosszabb. „A 3D nyomtatási technológia többszörösére, több hónapra csökkenti az időtartamot” - jegyzi meg Alekszej Kondratyev, a haditengerészet szakértője. - A tervezők időt spórolhatnak a rajzokon, amikor 3D -s modellt terveznek számítógépen, és azonnal elkészítik a kívánt alkatrész prototípusát. Nagyon gyakran az alkatrészeket az elvégzett tesztek figyelembevételével és a felülvizsgálat során újrafeldolgozzák. Ebben az esetben az alkatrész helyett elengedheti a szerelvényt, és ellenőrizheti az összes mechanikai jellemzőt, hogy az alkatrészek hogyan hatnak egymásra. Végső soron a prototípus -készítés időzítése lehetővé teszi a tervezők számára, hogy lerövidítsék az első kész minta tesztelési szakaszba való teljes idejét. Manapság körülbelül 15-20 évbe telik egy új generációs nukleáris tengeralattjáró létrehozása: a vázlattól az utolsó csavarig az összeszerelés során. Az ipari háromdimenziós nyomtatás továbbfejlesztésével és az alkatrészek tömeggyártásának ilyen módon történő elindításával az időkeret legalább 1,5-2-szeresére csökkenthető."
Szakértők szerint a modern technológiák mára egy -két évig tartanak a titán alkatrészek 3D nyomtatón történő tömeges gyártásától. Nyugodtan mondhatjuk, hogy 2020 végéig a katonai-ipari komplexum vállalatainál a katonai képviselők olyan berendezéseket fogadnak el, amelyeket 30-50% -ban 3D nyomtatási technológiák segítségével szerelnek össze. Ugyanakkor a tudósok számára a legnagyobb jelentőségű kerámia alkatrészek 3D nyomtatón történő létrehozása, amelyek nagy szilárdsággal, könnyűséggel és hővédő tulajdonságokkal rendelkeznek. Ezt az anyagot nagyon széles körben használják az űr- és légiiparban, de még nagyobb mennyiségben is használható. Például egy kerámia motor létrehozása 3D nyomtatón megnyitja a horizontot a hiperszonikus repülőgépek létrehozásához. Ilyen motorral egy személyrepülőgép pár óra alatt el tud repülni Vlagyivosztokból Berlinbe.
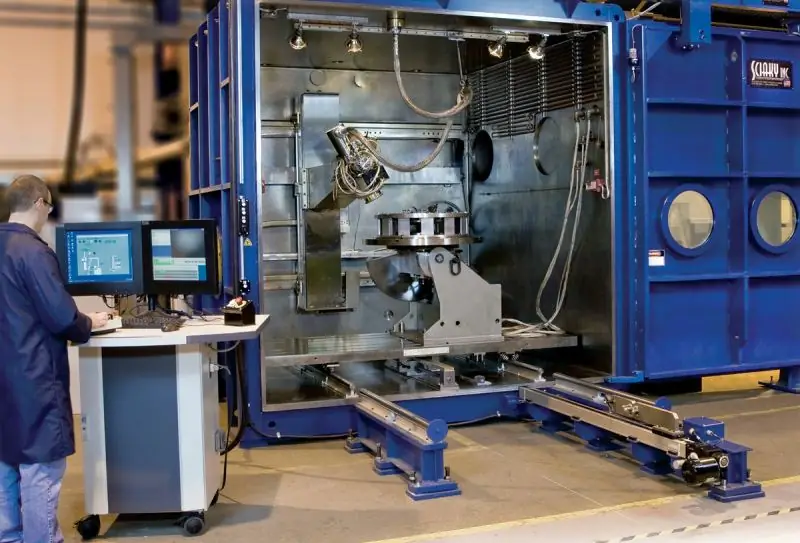
Azt is közölték, hogy amerikai tudósok kitaláltak egy gyantaformulát, amelyet kifejezetten 3D nyomtatókban való nyomtatáshoz használtak. Ennek a képletnek az értéke a belőle nyert anyagok nagy szilárdságában rejlik. Például egy ilyen anyag ellenáll a kritikus hőmérsékletnek, amely meghaladja az 1700 Celsius fokot, ami tízszer magasabb, mint sok modern anyag ellenállása. Stephanie Tompkins, a fejlett védelmi kutatásokért felelős tudományos igazgató becslései szerint a 3D -s nyomtatókkal létrehozott új anyagok egyedi jellemzők és tulajdonságok kombinációjával fognak rendelkezni. Az új technológiának köszönhetően Tompkins azt mondja, hogy képesek leszünk egy tartós, könnyű és hatalmas alkatrészt gyártani. A tudósok úgy vélik, hogy a kerámia alkatrészek 3D nyomtatón történő előállítása tudományos áttörést jelent, beleértve a polgári termékek gyártását is.
Az első orosz 3D műhold
Jelenleg a 3D nyomtatási technológia már sikeresen gyárt alkatrészeket közvetlenül az űrállomások fedélzetén. A hazai szakértők azonban úgy döntöttek, hogy még tovább mennek, azonnal úgy döntöttek, hogy létrehoznak egy mikroszatellitet 3D nyomtató segítségével. A Rocket and Space Corporation Energia létrehozott egy műholdat, amelynek testét, konzolját és számos más részét 3D -ben nyomtatták. Ugyanakkor fontos pontosítás, hogy a mikroszatellitet az Energia mérnökei a Tomszki Politechnikai Egyetem (TPU) hallgatóival közösen hozták létre. Az első nyomtató műhold a "Tomsk-TPU-120" teljes nevet kapta (a 120-as szám a névben az egyetem 120. évfordulója tiszteletére, amelyet 2016 májusában ünnepeltek). 2016 tavaszán a Progress MS-02 űrszondával együtt sikeresen felbocsátották az űrbe, a műholdat az ISS-hez szállították, majd az űrbe bocsátották. Ez az egység a világ első és egyetlen 3D műholdja.
A TPU hallgatók által létrehozott műhold a nanosatellites (CubSat) osztályába tartozik. A következő méretek: 300x100x100 mm. Ez a műhold volt a világon az első űrhajó, amelynek 3D nyomtatott teste volt. A jövőben ez a technológia valódi áttöréssé válhat a kis műholdak létrehozásában, valamint hozzáférhetőbbé és szélesebb körűvé teheti használatukat. Az űrhajó tervezését a TPU "Modern termelési technológiák" Tudományos és Oktatási Központjában dolgozták ki. Azokat az anyagokat, amelyekből a műhold készült, a Tomszki Politechnikai Egyetem és az Orosz Tudományos Akadémia Szibériai Fiókja Erőfizikai és Anyagtudományi Intézetének tudósai készítették. A műhold fő célja az űranyag -tudomány új technológiáinak tesztelése volt; ez segíteni fogja az orosz tudósokat a Tomszki Egyetem és partnerei számos fejlesztésének tesztelésében.
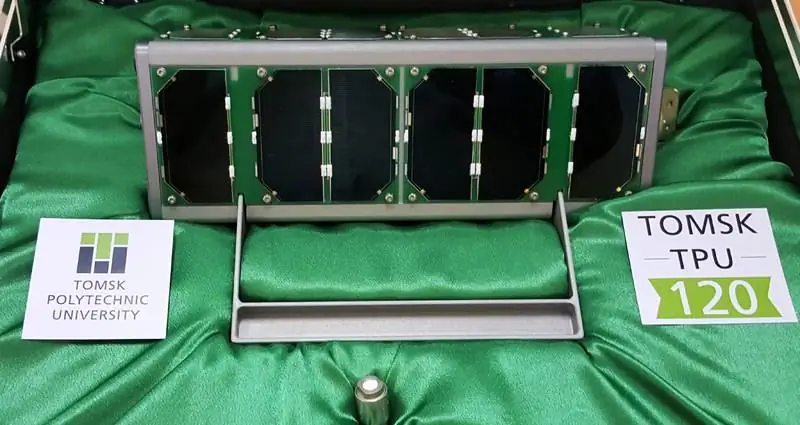
Az egyetem sajtószolgálata szerint a Tomszk-TPU-120 nanosatelit felbocsátását az ISS űrsétája során tervezték végrehajtani. A műhold meglehetősen kompakt, de ugyanakkor teljes értékű űrhajó, amely elemekkel, napelemekkel, fedélzeti rádióberendezésekkel és más eszközökkel van felszerelve. A fő jellemzője azonban az volt, hogy teste 3D nyomtatással készült.
A nanosatellite különféle érzékelői rögzítik a fedélzeten, az elemeken és a táblákon lévő hőmérsékletet és az elektronikus alkatrészek paramétereit. Ezt az információt ezután online továbbítják a Földre. Ezen információk alapján az orosz tudósok képesek lesznek elemezni a műholdas anyagok állapotát, és eldönteni, hogy felhasználják -e azokat a jövőben az űrhajók fejlesztésében és építésében. Meg kell jegyezni, hogy a kis űreszközök fejlesztésének fontos szempontja az ipar új személyzetének képzése is. Ma a Tomszki Politechnikai Egyetem hallgatói és tanárai saját kezűleg fejlesztenek, gyártanak és javítanak mindenféle kis űrhajó kivitelét, miközben nemcsak kiváló minőségű alapvető ismereteket, hanem a szükséges gyakorlati készségeket is elsajátítják. Ez teszi az oktatási intézmény végzőseit egyedülálló szakemberekké a jövőben.
Az orosz tudósok és az ipar képviselőinek jövőbeli tervei között szerepel az egyetemi műholdraj létrehozása. „Ma arról beszélünk, hogy motiválni kell diákjainkat, hogy tanulmányozzanak mindent, ami valamilyen módon kapcsolódik az űrhöz - lehet energia, anyagok és új generációs motorok létrehozása stb. Korábban megbeszéltük, hogy az űr iránti érdeklődés az országban némileg elhalványult, de újraéleszthető. Ehhez nem is a diákpadról, hanem az iskolai padból kell kiindulni. Így elindultunk a CubeSat - kis műholdak - fejlesztésének és gyártásának útjára” - jegyzi meg a Tomszki Politechnikai Intézet sajtószolgálata e felsőoktatási intézmény rektorára, Peter Chubikra hivatkozva.