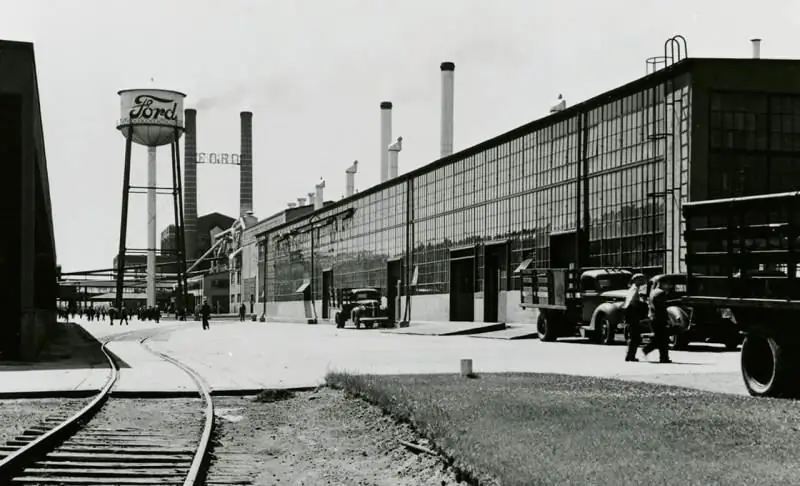
Stratégiai technológiák
Mielőtt megismerkedne a páncélozott gyártás jellemzőivel a michigani Ford detroiti gyárában (USA), érdemes röviden elmagyarázni azokat a feltételeket, amelyek mellett a páncélipar létrejött a Szovjetunióban. Mint tudod, minden összehasonlítás útján tanulható.
A második világháború alatti páncélgyártás volt az egyik legfontosabb stratégiai előny. A háború kezdetével a Szovjetunió katasztrofális helyzetbe került - minden páncélozott termelés az ország európai részére koncentrálódott. A német hadsereg gyors előretörése teljesen megbéníthatja a tankpáncélok gyártását az országban. Csak a háború elején keletkezett gyárak egy részének evakuálására irányuló hihetetlen erőfeszítések árán lehetett helyreállítani a páncélzatot. A fő "páncélozott gyárak" Kuznyeck, Nyizsnyij Tagil és Magnitogorsk kohászati üzemei voltak.
De az ügy nem korlátozódott a termelés egyszerű áthelyezésére a frontvonal mögötti új telephelyre. A legtöbb új gyár nem volt alkalmazkodva a harckocsipáncélok olvasztásához - a háború előtt a gyárak a Vasfém Népbiztosság igényeinek megfelelően dolgoztak. A Wartime hozzáigazította saját beállításait. Most a nyitott kandalló kemencékben gyakran voltak alacsonyan képzett munkások, akut probléma volt a speciális hő-, prés- és fémmegmunkáló berendezések hiánya. Ezért a páncélgyártás átadása magával a katonai acél olvasztására szolgáló technológia komoly átalakításával járt. Tehát a termelést hozzá kellett igazítani a fő nyitott kandalló kemencékhez 120-180 tonnára, kizárva a diffúziós dezoxidációs folyamatot. A páncéllemezek és páncélrészek keményítését vízben kellett elvégezni.
Egy ilyen egyszerűsítés nem befolyásolhatta a kapott páncél minőségét. Ez különösen igaz a legnehezebben gyártható nagy keménységű 8C tartályacélra. A páncéllemezek legelső mintái a tesztek során jelentős pala és rétegződést mutattak, magas hajlamúak a repedések kialakulására a hegesztés és az egyenesítés során. Ezenkívül a terepi tesztek a páncélminták túlzott törékenységét tárták fel a kagyló tüze során.
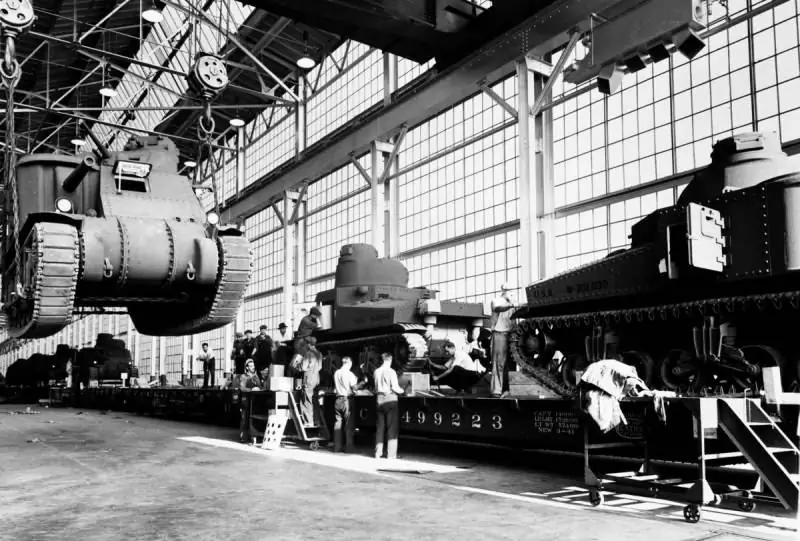
Az ilyen hibákat nem lehetett figyelmen kívül hagyni. A speciális TsNII-48-ban pedig számos fejlesztést fejlesztettek ki. Először is, mostantól kezdve a páncélacélt csak előmelegített kemencékben kellett olvasztani, miután "polgári" minőségű acélokat olvasztottak. Az acélt legalább másfél órán át kellett forralni a kandallós olvasztófürdőben, majd négyzet alakú vagy domború formákba önteni. Ezenkívül a kohászok különös figyelmet fordítottak az eredeti nyersvas kéntartalmára (legfeljebb 0,06%), valamint a szénre és a mangánra. Más intézkedésekkel együtt ez lehetővé tette a páncél minőségének javítását. Különösen a pala és a törés rétegzettségének csökkentése érdekében.
Fontos probléma volt a háztartási páncélok hőkezelésének technológiája. Egyszerűen fogalmazva, a páncéllemezek edzése és temperálása túl sok időt és energiát vett igénybe, és hiányzott a szükséges felszerelés. Szükséges volt a folyamat egyszerűsítésére. Ezzel kapcsolatban egy tipikus példát hozunk.1942-ben a TsNII-48 kohászainak sikerült annyira leegyszerűsíteniük a termikus előkészítés folyamatát, hogy csak a KV és a T-34 tartályok aljának egyes részeihez körülbelül 3230 kemenceórát mentettek meg 100 hajótestenként.
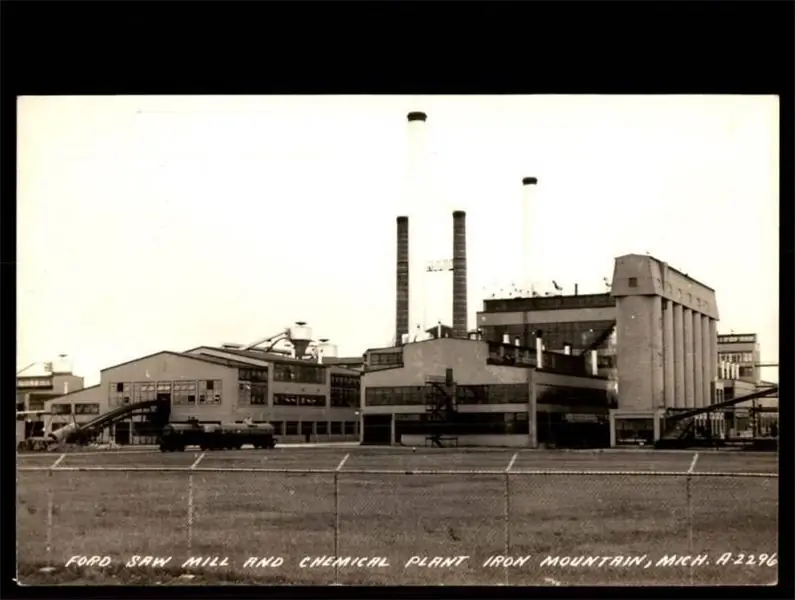
Ennek ellenére a Szovjetunió háborújának végéig a stratégiai fontosságú harckocsipáncélok előállításának feltételei messze nem voltak szükségesek. Ugyanez nem mondható el a tengerentúli partner hadiiparáról, amelynek területét nem érintette a világháború. A szovjet kohászati mérnököknek 1945. február 26 -án, 72 nappal a győzelem előtt ismét meg kellett győződniük erről.
Amerikai luxus
A szovjet küldöttségnek a Ford páncélosgyárba tett látogatásának kevéssé ismert történetét Vaszilij Vlagyimirovics Zapariy, az Orosz Tudományos Akadémia uráli ágának Történelem és Régészet Intézetének történettudományi kandidátusa jelentette be. A tudós anyaga a szovjet kohászok jelentésén alapul, amely az orosz állam gazdasági archívumában (RGAE) tárolt egyesült államokbeli utazás eredményeiről készült. Meg kell jegyezni, hogy az RGAE csupán a Nagy Honvédő Háború korszakából származó levéltári dokumentumok kincsesbányája, amelyek katonai felszerelések és felszerelések gyártásával kapcsolatosak. Csak találgatni kell, hogy az archívum még hány titkot őriz az eddig minősített bizonyítékokban.
A Detroitból hazatért mérnökök szerint a Ford gyár páncélozott műhelye két, 273 méter hosszú, 30 méter széles és körülbelül 10 méter magas átmérőjű épület volt. Ugyanakkor a bolt nem szagolt páncélt. Elsősorban acélok hőkezelésére és vágására szánták. Ez természetesen különleges érdeklődést váltott ki a szovjet kohászok körében, tekintettel a hazai páncélozott gyártás fent leírt problémáira. A Ford Motors műhely fő gyártási profilja 76 mm vastag páncélzatokkal dolgozott. Hőkezelt acéllemezeket használtak a könnyű és közepes páncélozott járművek házának hegesztésére más detroiti gyárakban.
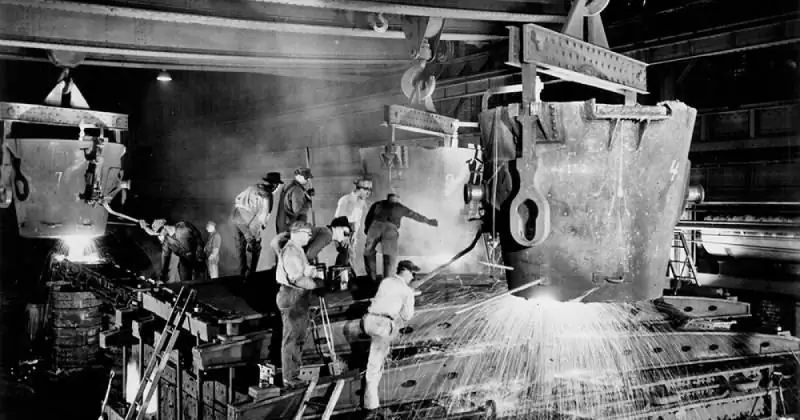
Először is, a gyártási folyamat gépesítése lenyűgözte a Ford műhelyeit. Olvadás és hengerlés után a páncéllemezeket a United hidraulikus asztali rakodókkal szállították a hőkezelő műhelybe. A rakodók pedig a műhely közelében található vasúti peronokról vitték el a páncélt. Magában a műhelyben két híddaru volt a páncéllemezek mozgatására, minden technológiai művelet során, kivéve a keményedési folyamatokat.
A páncél szükséges kristályos szerkezetének megteremtéséhez két, egyenként 2500 tonna erőfeszítésű prést, öt 70 méteres szállítószalag módszertani kemencét és öt 100 méteres gáz-temperáló szállítószalag kemencét hívtak fel. A vizet a páncél keményítő présekhez egyszerre hat szivattyú működtette, percenként több mint 3700 liter szivattyúzással. Ahogy orosz mérnökök írták, az ilyen prések tervezésének összetettsége és költsége, amelyek egyszerre képesek pecsételni és lehűteni a vörös-forró páncélt, megfizethetetlenek voltak. Ugyanakkor kétségek merültek fel a 30-76 mm vastagságú páncélokhoz való préselés célszerűségével kapcsolatban. Itt a hűtéshez szükséges vízellátás intenzitása került előtérbe.
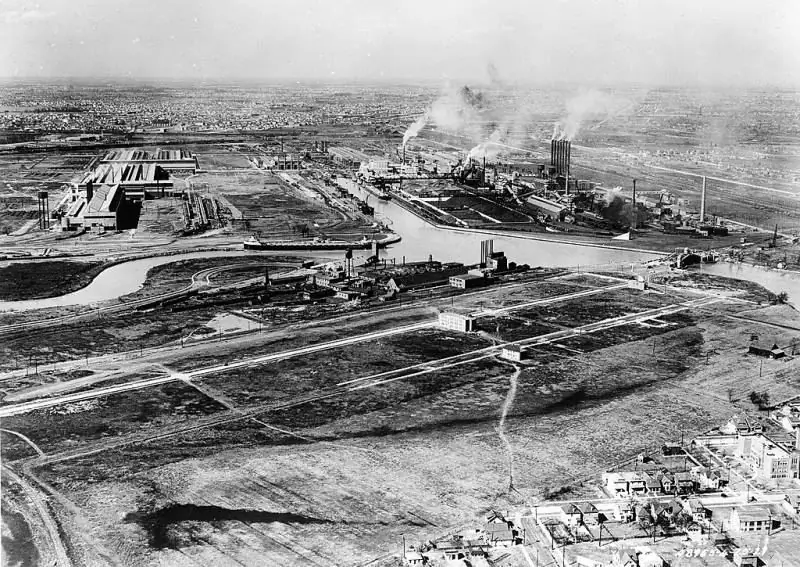
Nem a 2500 tonnás prések voltak az egyetlenek a Ford páncélozott járművében. A Toledo # 206 prések vékony páncélzat vágásával foglalkoztak, és 161 tonna nyomást fejlesztettek ki. A 2,5 cm -nél vastagabb páncéloknál kizárólag tűzvágást használtak.
A vállalkozásban tett látogatás során a kohászok megragadhatták a vékony golyóálló páncél keményedésének folyamatát. 15 másodpercig 1000 tonnás prés alatt maradt, majd a lapot 2,5 órára küldték 900 Celsius fokos lehűlésre és négy órányi vakációra 593 fokon.
Mindezt a technikai gazdagságot a szovjet mérnökök figyelték meg, nem számítva a különféle "apró tartozékokat": hegesztőgépeket, marógépeket, ollókat és hasonlókat.
A páncél hőkezelésének fő jellemzője a folyamatos gyártás volt. A feldolgozás szinte minden szakaszában az acéllemezek görgős és láncos szállítószalagokon mozogtak. A szállítószalagot egy központi konzolról vezérelték. Az utolsó szakaszok egyikén minden páncéllemezt megvizsgáltak a Brinell keménység szintjén. Ebben az esetben a vizsgálati paraméter ingadozása lapról lapra minimális legyen - legfeljebb 0,2 mm.
A szovjet delegáció számára különösen érdekes volt két lövöldöző robbantógép, amelyek szinte minden technológiai művelet után megtisztították a páncéllemezeket. Ilyen perfekcionizmust és ilyen luxust csak az amerikaiak engedhettek meg maguknak, távol a háborús nehézségektől.