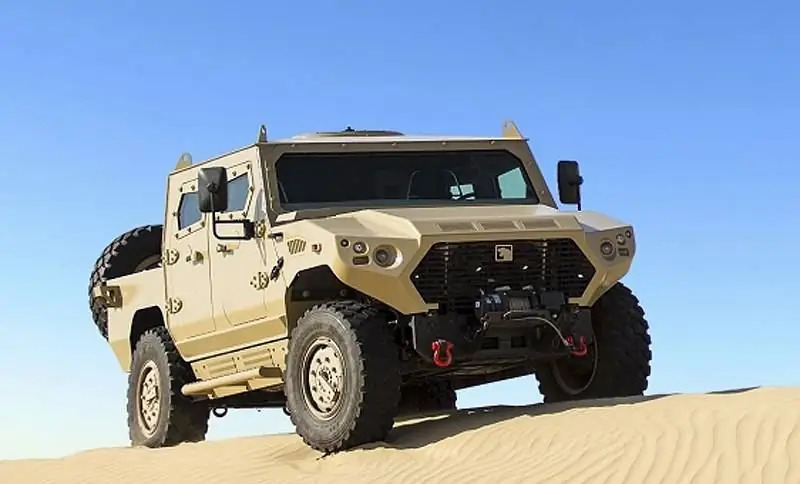
A páncél több millió évvel idősebb az emberiségnél, és elsősorban az állkapcsok és karmok elleni védelemre fejlesztették ki. Lehetséges, hogy a krokodilok és a teknősök részben inspirálhatják az embereket védőelemek létrehozására. Minden mozgási energia fegyver, legyen az őskori ütő vagy páncéltörő lövedék, úgy van kialakítva, hogy nagy erőt összpontosítson egy kis területen, feladata, hogy behatoljon a célba, és maximális sebzést okozzon rajta. Következésképpen a páncél feladata ennek megakadályozása a támadóeszközök elterelésével vagy megsemmisítésével és / vagy a becsapódási energia minél nagyobb területen történő szétszórásával annak érdekében, hogy minimálisra csökkentse a munkaerő, a szállítási rendszerek és az általa védett szerkezetek károsodását.
A modern páncélzat jellemzően egy kemény külső rétegből áll, amely megállítja, eltereli vagy megsemmisíti a lövedéket, egy közbenső rétegből, amelynek nagyon magas a „törési munkája”, és egy viszkózus belső rétegből, hogy megakadályozza a repedéseket és törmeléket.
Acél
Az acél, amely az első olyan anyag lett, amelyet széles körben használtak a páncélozott járművek gyártásában, még mindig keresett, annak ellenére, hogy alumínium és titán könnyű ötvözetein alapuló páncélok, kerámiák, polimer mátrixú, üvegszálakkal megerősített kompozitok, aramidok jelentek meg és ultra-nagy molekulatömegű polietilén, valamint fém mátrixú kompozit anyagok.
Sok acélgyár, köztük az SSAB, továbbra is nagyszilárdságú acélokat fejleszt különféle súlykritikus alkalmazásokhoz, például kiegészítő burkolathoz. Páncélozott acél minőségű ARM OX 600T, 4-20 mm vastagságban kapható, garantált keménységgel 570-640 HBW egység (keménység, Brinell, Wolfram rövidítése; teszt, amelyben szabványos átmérőjű volfrámgolyót préselnek) ismert erővel rendelkező anyagmintába, majd a kialakított mélyedés átmérőjét mérik, majd ezeket a paramétereket behelyettesítik a képletbe, amely lehetővé teszi a keménységegységek számának meghatározását).
Az SSAB hangsúlyozza a keménység és a szívósság megfelelő egyensúlyának elérésének fontosságát is a behatolás és a repedésvédelem szempontjából. Mint minden acél, az ARMOX 600T vasból, szénből és számos más ötvöző komponensből áll, beleértve a szilíciumot, mangánt, foszfort, kénet, krómot, nikkelt, molibdént és bórt.
Az alkalmazott gyártási technikáknak korlátai vannak, különösen a hőmérséklet tekintetében. Ez az acél nem alkalmas további hőkezelésre; ha a szállítás után 170 ° C fölé melegítik, az SSAB nem tudja garantálni tulajdonságait. Azok a vállalatok, amelyek meg tudják kerülni ezt a fajta korlátozást, valószínűleg vonzzák a páncélozott járműgyártók alapos vizsgálatát.
Egy másik svéd cég, a Deform golyóálló páncélacél forró formájú alkatrészeket kínál páncélozott járműgyártóknak, különösen azoknak, akik javítani kívánják a haszongépjárművek / polgári járművek védelmét.
Egy darabból álló Deform tűzfalak vannak felszerelve a Nissan PATROL 4x4-be, a Volkswagen T6 TRANSPORTER mikrobuszba és az Isuzu D-MAX pickup-ba, ugyanabból az anyagból készült szilárd padlólemezzel. A Deform által kifejlesztett és a lemezgyártásban használt forróformázási eljárás 600HB [HBW] keménységet tart fenn.
A vállalat azt állítja, hogy vissza tudja állítani a piacon található összes páncélcél tulajdonságait, miközben fenntartja a szerkezetileg meghatározott formát, miközben az így kapott alkatrészek sokkal jobbak, mint a hagyományos hegesztett és részben átfedő szerkezetek. A Deform által kifejlesztett módszernél a lemezeket forró kovácsolás után edzik és edzik. Ennek a folyamatnak köszönhetően olyan háromdimenziós alakzatokat lehet kapni, amelyeket hideg formázással nem lehet megszerezni a kötelező ilyen esetekben "hegesztések, amelyek megsértik a kritikus pontok integritását".
A deformált, melegen formázott acéllemezeket a BAE Systems BVS-10 és CV90, valamint az 1990-es évek eleje óta számos Kraus-Maffei Wegmann (KMW) gépen alkalmazták. Megrendelések érkeznek a LEOPARD 2 tartályhoz készült háromdimenziós páncéllemezek, valamint a BOXER és a PUMA járművek több formájú lemezének gyártására, valamint számos Rheinmetall járműre, köztük ismét a BOXER-re, valamint a WIESEL jármű fedelére. A Deform más védőanyagokkal is működik, beleértve az alumíniumot, a kevlárt / aramidot és a titánt.
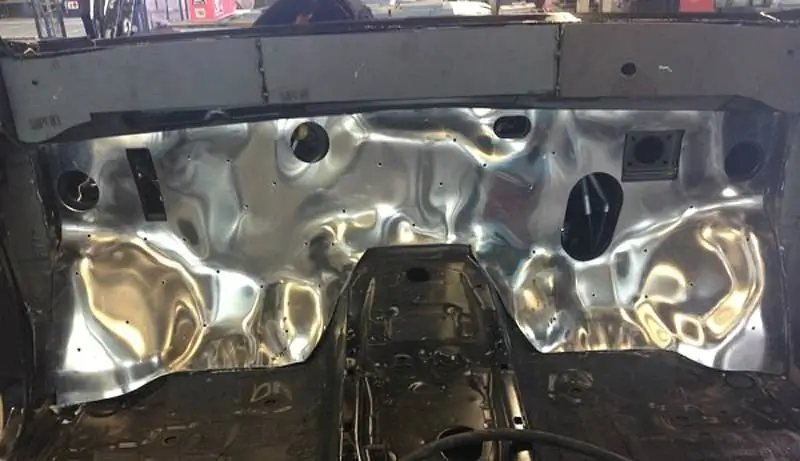
Az alumínium fejlődése
Ami a páncélozott járműveket illeti, először az alumínium páncélt széles körben használták az 1960 óta gyártott M113 páncélozott szállítójármű gyártásában. 5083 jelzésű ötvözet volt, amely 4,5% magnéziumot és jóval kisebb mennyiségű mangánt, vasat, rézt, szenet, cinket, krómot, titánt és más anyagokat tartalmazott. Bár az 5083 hegesztés után is megőrzi szilárdságát, nem hőkezelt ötvözet. Nem rendelkezik olyan jó ellenállással a 7,62 mm-es páncéltörő golyókkal szemben, de-amint azt a hivatalos tesztek megerősítették-a 14,5 mm-es szovjet stílusú páncéltörő golyókat jobban megállítja, mint az acél, miközben tömeget takarít meg és növeli a kívánt erőt. Az ilyen szintű védelem érdekében az alumíniumlemez vastagabb és 9 -szer erősebb, mint az acél, alacsonyabb sűrűsége 265 r / cm3, ami a szerkezet súlyának csökkenését eredményezi.
A páncélozott járműgyártók hamarosan könnyebb, ballisztikusan erősebb, hegeszthető és hőkezelhető alumínium páncélt kezdtek kérni, ami az Alcan 7039-es, majd később 7017-es fejlesztését eredményezte, mindkettő magasabb cinktartalommal.
Akárcsak az acél esetében, a sajtolás és az azt követő összeszerelés is negatívan befolyásolhatja az alumínium védő tulajdonságait. Hegesztéskor a hő által érintett zónák lágyulnak, de szilárdságuk részben helyreáll a természetes öregedés során bekövetkező megkeményedés miatt. A fém szerkezete a hegesztés közelében lévő keskeny zónákban megváltozik, nagy maradék feszültségeket okozva hegesztési és / vagy szerelési hibák esetén. Következésképpen a gyártási technikáknak minimálisra kell csökkenteni őket, miközben a feszültségkorróziós repedések kockázatát is minimalizálni kell, különösen akkor, ha a gép tervezett élettartama több mint három évtized.
A feszültségkorróziós repedések korróziós környezetben repedések megjelenésének és növekedésének folyamata, amely az ötvöző elemek számának növekedésével romlani szokott. A repedések kialakulása és azok későbbi növekedése a hidrogén szemcseszegély mentén történő diffúziója következtében következik be.
A repedésre való hajlam meghatározása a repedésekből kis mennyiségű elektrolit kivonásával és elemzésével kezdődik. Alacsony igénybevételi sebességű feszültségkorróziós teszteket végeznek annak megállapítására, hogy egy adott ötvözet mennyire sérült meg. Két minta mechanikus nyújtása (az egyik korrozív környezetben, a másik száraz levegőben) meghibásodásig történik, majd összehasonlítják a törés helyén tapasztalható plasztikai deformációt - minél jobban nyúlnak a mintához, annál jobb.
A feszültségkorróziós repedésekkel szembeni ellenálló képesség javítható a feldolgozás során. Például a Total Materia szerint, amely „a világ legnagyobb anyag -adatbázisának” nevezi magát, az Alcan 40 -szeresére javította a 7017 teljesítményét a gyorsított feszültségkorróziós repedések vizsgálatában. A kapott eredmények lehetővé teszik a hegesztett szerkezetek olyan zónáinak korrózióvédelmi módszereinek kidolgozását is, amelyekben nehéz elkerülni a maradék feszültségeket. Folyamatban van az ötvözetek javítására irányuló kutatás a hegesztett kötések elektrokémiai jellemzőinek optimalizálása érdekében. Az új hőkezelhető ötvözetek kidolgozása erősségük és korrózióállóságuk javítására összpontosít, míg a nem hőkezelhető ötvözeteken végzett munka célja a hegeszthetőségi követelmények által támasztott korlátok megszüntetése. A fejlesztésben lévő legkeményebb anyagok 50% -kal erősebbek lesznek, mint a jelenleg használt legjobb alumínium páncélok.
Az alacsony sűrűségű ötvözetek, mint például a lítium -alumínium, körülbelül 10% tömegmegtakarítást eredményeznek a hasonló golyóállósággal rendelkező ötvözetekkel szemben, bár a ballisztikus teljesítményt még nem kell teljes mértékben értékelni a Total Materia szerint.
A hegesztési módszerek, beleértve a robotokat is, javulnak. A megoldandó feladatok között szerepel a hőellátás minimalizálása, az energia- és huzalellátó rendszerek fejlesztésének köszönhetően stabilabb hegesztési ív, valamint a folyamat szakértői rendszerek általi felügyelete és ellenőrzése.
Az MTL Advanced Materials az ALCOA Defense nevű, neves alumínium páncéllemezgyártóval dolgozott együtt, hogy kifejlessze azt, amit a vállalat "megbízható és megismételhető hidegformázási folyamatként" ír le. A vállalat megjegyzi, hogy a páncélos alkalmazásokhoz kifejlesztett alumíniumötvözeteket nem hidegen formázásra tervezték, vagyis új eljárása segít elkerülni a gyakori meghibásodási módokat, beleértve a repedéseket is. A végső cél az, hogy a géptervezők minimalizálják a hegesztés szükségességét és csökkentsék az alkatrészek számát a vállalat szerint. A vállalat hangsúlyozza, hogy a hegesztési mennyiség csökkentése növeli a szerkezeti szilárdságot és a személyzet védelmét, miközben csökkenti a gyártási költségeket. A jól bevált 5083-H131 ötvözetből kiindulva a vállalat kifejlesztett egy eljárást hidegen formázó alkatrészekhez, amelyek 90 fokos hajlítási szöggel rendelkeznek a szemek mentén és azokon keresztül, majd továbbléptek az összetettebb anyagokhoz, például a 7017, 7020 és 7085 ötvözetekhez, jó eredményeket is elérni.
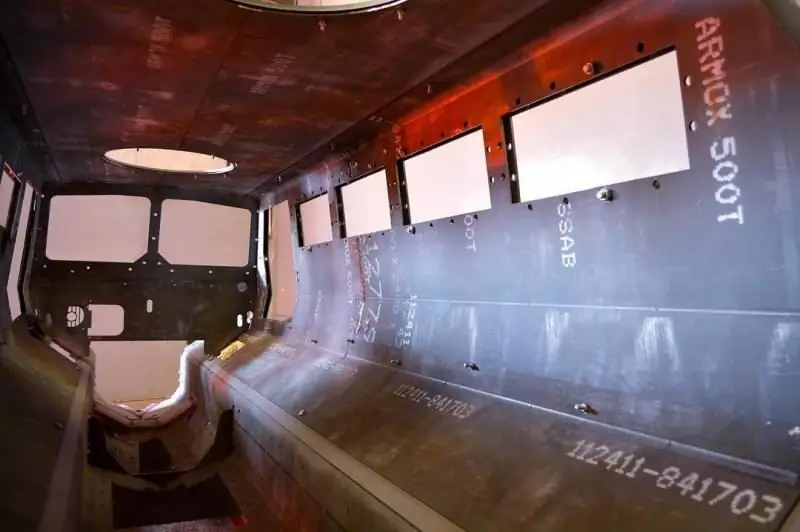
Kerámiák és kompozitok
Néhány évvel ezelőtt a Morgan Advanced Materials bejelentette számos SAMAS páncélrendszer kifejlesztését, amelyek fejlett kerámiák és szerkezeti kompozitok kombinációjából álltak. A termékcsalád csuklós páncélzatot, töredezésgátló béléseket, szerkezeti kompozitokból készült túlélési kapszulákat tartalmaz, amelyek fémtest cseréjére és fegyveres modulok védelmére szolgálnak, mind lakottan, mind lakatlanul. Mindegyik egyedi igényekhez igazítható, vagy megrendelésre készül.
STANAG 4569 2-6 szintű védelmet nyújt, több ütéses teljesítmény és súlymegtakarítás mellett (a vállalat állítása szerint ezek a rendszerek fele akkora súlyúak, mint a hasonló acéltermékek), és alkalmazkodnak a konkrét veszélyekhez, platformokhoz és küldetésekhez. … A repedésgátló bélések 12,3 kg súlyú lapos panelekből készülhetnek 0,36 m2 (kb. 34 kg / m2) területre, vagy 12,8 kg súlyú szilárd szerelvények 0,55 m2-re (kb. 23,2 kg / m2).
A Morgan Advanced Materials szerint az új és a meglévő platformok korszerűsítésére tervezett kiegészítő páncélzat a súly felével azonos képességeket kínál. A szabadalmaztatott rendszer maximális védelmet nyújt a fenyegetések széles skálájával szemben, beleértve a kis- és közepes kaliberű fegyvereket, a robbanószerkezeteket (IED) és a rakétahajtású gránátokat, valamint a többütéses teljesítményt.
A "félszerkezeti" páncélrendszert jó korrózióállósággal kínálják a fegyvermodulokhoz (a légi és tengeri alkalmazások mellett), és a súlymegtakarítás és a súlypont minimalizálása mellett, az acéllal ellentétben kevesebb elektromágneses kompatibilitási problémát okoz.
A fegyvermodulok védelme különös problémát jelent, mivel vonzó célpont, mivel letiltásuk drasztikusan rontja a személyzet helyzeti irányítását és a jármű képességét a közeli fenyegetések kezelésére. Finom optoelektronikával és sérülékeny villanymotorokkal is rendelkeznek. Mivel ezeket általában a jármű tetejére szerelik fel, a páncélzatnak könnyűnek kell lennie, hogy a súlypont a lehető legalacsonyabb legyen.
A fegyvermodulok védelmi rendszere, amely tartalmazhat páncélozott üveget és a felső rész védelmét, teljesen összecsukható, két ember 90 másodperc alatt összeállíthatja. A kompozit túlélési kapszulák abból készülnek, amit a vállalat „egyedi kemény anyagokból és polimer készítményekből” ír le, repeszvédelmet nyújtanak, és javíthatók a területen.
Katona védelem
A 3M Ceradyne által kifejlesztett SPS (katonavédelmi rendszer) sisakokat és testpáncélbetéteket tartalmaz az integrált fejvédelmi rendszerhez (IHPS) és a VTP -hez (Vital Torso Protection). kézi lőfegyverek).
Az IHPS követelményei közé tartozik a kisebb súly, a passzív hallásvédelem és a jobb tompa ütésvédelem. A rendszer olyan tartozékokat is tartalmaz, mint például a katona alsó állkapcsát védő alkatrész, védőablak, az éjjellátó szemüveg tartója, útmutatók például zseblámpához és fényképezőgéphez, valamint további moduláris golyóvédelem. A több mint 7 millió dollár értékű szerződés mintegy 5300 sisak szállítását írja elő. Időközben a 36 millió dolláros szerződés keretében több mint 30.000 ESAPI készletet szállítanak - könnyebb betéteket testpáncélhoz. Mindkét készlet gyártása 2017 -ben kezdődött.
Szintén az SPS program keretében a KDH Defense kiválasztotta a Honeywell SPECTRA SHIELD és GOLD SHIELD anyagait öt alrendszerhez, beleértve az SPS projekthez szállítandó Torso és Extremity Protection (TEP) alrendszert. A TEP védelmi rendszer 26% -kal könnyebb, ami végül 10% -kal csökkenti az SPS rendszer súlyát. A KDH az UHMWPE szálon alapuló SPECTRA SHIELD -t és az aramidszálakon alapuló GOLD SHIELD -t fogja használni ehhez a rendszerhez.
SPECTRA szál
A Honeywell szabadalmaztatott polimer szál fonási és húzási eljárást alkalmaz az UHMWPE nyersanyag SPECTRA szálba ágyazásához. Ez az anyag súlyát tekintve tízszer erősebb az acélnál, fajlagos szilárdsága 40% -kal magasabb, mint az aramidszálé, olvadáspontja magasabb, mint a hagyományos polietiléné (150 ° C), és nagyobb kopásállósággal rendelkezik, mint más polimerek, például poliészter.
Az erős és merev SPECTRA anyag nagy deformációt mutat töréskor, vagyis nagyon erősen nyújtódik törés előtt; ez a tulajdonság lehetővé teszi nagy mennyiségű ütési energia elnyelését. A Honeywell azt állítja, hogy a SPECTRA szálas kompozitok nagyon jól teljesítenek nagy sebességű ütések, például puskagolyók és lökéshullámok esetén. A vállalat szerint: „Fejlett szálunk úgy reagál az ütésekre, hogy gyorsan eltávolítja a mozgási energiát az ütközési zónából … jó rezgéscsillapítással, jó ellenállással az ismételt deformációkkal szemben, valamint a szálak kiváló belső súrlódási jellemzőivel, valamint kiváló vegyszerállósággal., víz és UV fény."
A SHIELD technológiájában a Honeywell párhuzamos szálakat terít szét, és fejlett gyantával impregnálva összeragasztja őket, hogy egyirányú szalagot hozzon létre. Ezután ennek a szalagnak a rétegeit keresztben, a kívánt szögben, adott hőmérsékleten és nyomáson helyezik el, és összetett szerkezetbe forrasztják. Puha, hordható alkalmazásokhoz két réteg vékony és rugalmas átlátszó fólia közé laminálják. Mivel a szálak egyenesek és párhuzamosak maradnak, hatékonyabban oszlatják el az ütési energiát, mintha szőtt anyagba szőnék.
A Short Bark Industries SPECTRA SHIELD -t is használ az SPS TEP rendszer BCS (Ballistic Combat Shirt) testőrében. A Short Bark lágy védelemre, taktikai ruházatra és kiegészítőkre specializálódott.
Honeywell szerint a katonák az ezekből az anyagokból készült védőelemeket választották, miután kiváló teljesítményt mutattak aramidszálas társaikkal szemben.